Variable Primary Flow Design in Chiller
- Scholenberg
- Dec 12, 2021
- 7 min read
Updated: Jan 14, 2022
Modern DDC controllers on chillers allow the possibility of variable flow design. Traditional thinking has been that the chiller should see the constant flow and then the load will vary directly with the return fluid temperature. Allowing variable flow means the cooling load can vary either with the return fluid temperature or a change in the chilled water flow. It requires modern controllers to deal with two variables and provide stable chiller operation.
Figure 62 shows a two chiller variable primary flow system. Variable primary flow can be applied to single, parallel, or series chiller plants although parallel is the most common. The control valve at the cooling loads is a two-way type so the chilled water flow varies with the cooling load. The primary pump for the chillers circulates the chilled water throughout the building. The chilled water flow varies through the chillers as well. This is the main difference between variable primary flow and primary/secondary flow
Variable primary flow provides pump savings over primary-secondary systems because all the chilled water being pumped is being used for cooling. In a primary-secondary system, any flow through the decoupler consumes pump power but provides no cooling. There is a bypass line to maintain minimum flow through the chillers only. Whenever the chilled water flow is above the minimum, the bypass is closed.
2.1 Chillers
Almost any type of chiller can be used including air-cooled and water-cooled. The chiller must have a unit controller capable of dealing with both a change in flow and a change in return temperature. In most cases, the controller should be a modern digital type, using a PID loop control. Check with the manufacturer whether the controller is capable of variable primary flow. Usually, the controller can be upgraded on an existing unit if required.
The range of flow rates in the chiller is limited at the low end by laminar flow in the tubes (2 to 3 fps tube velocity) and at the high end by tube erosion and vibration (10 to12 fps tube velocity). Chiller selection software typically tries to pick a tube velocity of around 6 fps, which provides a good balance between water pressure drop and heat transfer performance. Half the typical design flow rate will result in 3 fps tube velocities which are about the minimum. The actual minimum should be provided by the manufacturer and is often included in computer selections.
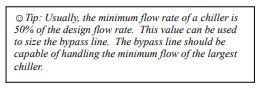
Selecting the chiller with tube velocities at design conditions near 10 fps allows the system flow to be turned down to 30% of the design flow. This may be advantageous where there is only one chiller in the system with few operating hours at design flow.
In most cases, the chillers will be the same size. The flow ranges and capacities must be carefully considered so that there are no operating points where no combination of chillers can meet the load. For example, if two evenly identical chillers have a minimum flow rate of 60% of design, there will be a “hole” between 50 and 60% of plant capacity. One chiller can meet the load up to 50% of plant capacity. However, at say 55% two chillers will be required but the flowrate will be less than the minimum required. Careful chiller selection (preferred since it is more energy efficient) and the use on the bypass will resolve this problem.
2.2 Pumps
The chilled water pump is variable flow (see Pumping Basics). They are sized to provide enough heads to circulate chilled water throughout the building. Automatic isolating valves are provided in front of each chiller to stop flow when the chiller is not operating. Pumps can be dedicated to each chiller or in the main return line, as shown in Figure 62. Common pumps allow over pumping and sharing a spare pump.
2.3 Bypass Line
The bypass should be sized for the minimum flow rate of the largest chiller being used. It is only used to provide minimum flow to a chiller when the flow requirement through the chiller plant is less than the chiller minimum flow.
The bypass line can be located between the chillers and the loads, as shown in Figure 62. This is the same location as the decoupler is in a conventional primary-secondary system. The bypass line could also be placed at the end of the cooling loop. The bypass control valves will see a smaller pressure drop but there may be some additional pump work.
Alternatively, some cooling loads could use three-way valves, which would provide the minimum flow required. On the other hand, these valves will bypass chilled water any time they are not operating at the design load, which wastes pump work and leads to low delta T syndrome. When flow is required through the bypass line, it must be controlled. A modulating two or three-way valve is required.
Although a variable primary flow system is no more difficult to design than a primary-secondary system, the control sequences must be carefully thought out and commissioned. A building automation system (BAS) capable of variable primary flow is a must. Direct communication between the BAS and the chiller unit controllers is strongly recommended as well. This can be accomplished with standard open control protocols such as BACnet or LonTalk
3.1 Primary Pump Control
The primary pump is controlled in the same manner as a secondary pump in a primary-secondary system (Refer to Pumping Basics).
Modulating both the flow and temperature range through a chiller requires time for the chiller controller to respond. Many factors influence the rate of change of the flow including the chiller type, the chiller controller logic, and the actual load on the chiller at the time. Some field adjustment of the rate of change time should be expected during commissioning. A good starting point is a 10% change in flow per minute. This will affect the modulating rate of the primary pumps and the terminal unit control valves.
3.2 Bypass Line Valve Control
It is recommended that each chiller should have a flow meter. The meter can be used to recognize both minimum and maximum flow constraints. Individual chiller meters allow each chiller’s flow rate to monitored, which may be advantageous in some chiller plant control concepts such as over pumping or deliberately operating multiple high part-load efficient chillers in lieu of a single chiller.
It is possible to use only one flow meter in the common chilled water supply line upstream of the bypass line. Assuming only one chiller is operating when minimum flow becomes an issue, the flow measured at this point would be the flow through the operating chiller.
The bypass line control valve is controlled by a signal from the flow meter of the operating chiller. The control system should recognize the chiller and know the minimum flow rate for that chiller. In most cases, the chillers are all the same, and hence there is only one minimum flow rate for the entire chiller plant. The bypass line control valve is modulated to maintain the minimum chiller flow. This must be done slowly. Fast changes in the bypass line flow may cause the primary pump control loop to hunt as it recognizes a change in total chilled water flow.
3.3 Starting an Additional Chiller
The first step is recognizing an additional chiller is required. The BAS can use the individual chiller flow meter and the chiller load as indicators that another chiller is required. Another chiller is required when either the chiller capacity or the chiller design flow rate has been reached.
Using the maximum flow rate rather than the design flow rate will “over pump” the chiller. The pressure drop will exceed design conditions and increase the primary pump work. The advantage of this is that starting another chiller and its ancillary equipment (condenser pump, cooling tower etc) is staved off. This is a good method for counteracting low delta T syndrome.
A different approach to this is to use chillers with excellent part-load performance and deliberately operate multiple chillers at part load. Refer to Low Delta T Syndrome. Adding a chiller is more complicated than other chiller plant systems as explained in the example below. Each chiller must have an automatic isolating valve. When the chillers are all the same size, the valves can be two-position type. These valves must open and close slowly.

To reduce the possibility of a nuisance trip, the following sequence is recommended. Prior to opening the isolating valve on the chiller to be started, use either the demand limiting feature or some form of controls communication to reduce the capacity of the operating chiller(s) to 50%. Next, slowly open the isolating valve on the chiller to be started. Enable the added chiller and allow it to start. Release the demand limiting on the original chiller(s). During the chiller startup, accurate chilled water supply temperature control will be lost for a few minutes. In most HVAC applications, this is acceptable. For close tolerance designs, a different concept may be required. There are other methods for adding chillers. The goal is to add the chiller and avoid a nuisance trip or damage to the equipment.
3.4 Shutting Down a Chiller
A chiller can be shut down when the sum of the chilled water flows through all the operating chillers is less than the design capacity of the remaining chiller(s). If the concept of using two efficient part-load chillers rather than one conventional chiller is being used, then one chiller is stopped when all chillers are at or below their minimum part-load percentage for a fixed time period; this period varies with application.
To shut down a chiller, the chiller is commanded off by the BAS. Once the chiller is off, its isolating valve is slowly closed. It is important to provide some time for the remaining chillers to ramp up to the additional load.
'
3.5 Variable Primary Flow with Different Sized Chillers
Using different sized chillers (and hence different chilled water flow rates,) in a variable primary flow system further increases the complexity. Providing the correct amount of chilled water flow to each chiller becomes an issue. Using dedicated variable flow primary pumps allows chiller specific flow control but creates pump selection and control issues.
If a common pumping plant is used for all chillers then the chiller isolating valves may need to be modulated to control the correct flow rate for each chiller. This may lead to a hunting problem between the valves and the primary pump.
The staging of chillers also becomes complex. Which size chiller should be added or subtracted must now be considered. Variable primary flow chiller plants with different sized chillers have been successfully designed and implemented but it is recommended that the value of different sized chillers be carefully weighed against the additional complexity.
4.0 Training and Commissioning
Variable primary flow systems are more difficult to commission than other chiller plant designs and this should not be ignored. All parties involved in the choice, design, commission, and operation of a variable primary flow system should understand this and be committed to a successful project. Operator training is especially important. It is critical to a successful installation that a thorough operator training program be part of the project.
Comments