DESIGN OF AIR COOLED CHILLERS
- Scholenberg
- Dec 6, 2021
- 7 min read
The choice of chiller type and chiller plant design are inherently linked. Different chiller types have different strengths and by careful selection of chiller plant design, these strengths can be optimized.
1.0 Air Cooled Chillers

Air-cooled screw chillers (Figure 28) range in capacity from 170 to 550 tons. These chillers offer very good performance, particularly at part load. The compressors are modulating rather than stepped which provides more accurate control especially if the chiller is equipped with a VFD.
Air-cooled chillers avoid the need for cooling towers, condenser pumps, and condenser piping which can offer substantial capital savings. Air-cooled chillers do not require mechanical room space which offers additional savings.

Another advantage of air-cooled chillers is they do not consume water like water-cooled chillers. A 400-ton chiller will consume over 700 gallons per hour to offset cooling tower makeup. Where water is scarce, this can be a significant cost. In addition, condenser water treatment is avoided.
Ambient sound levels must be carefully considered with air-cooled chillers. Both the condenser fans and compressors are sound sources. Manufacturers provide sound power and/or sound pressure data that can be used to estimate the sound levels at the property line or any other point where sound levels are an issue.
1.1 Dry-bulb Relief
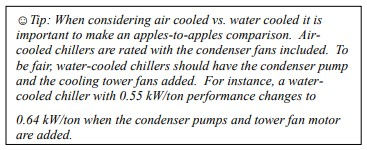
Air-cooled chillers have lower performance (consume more power) than water or evaporatively cooled chillers because of the increased lift. Refrigeration work is proportional to lift; doubling the lift will approximately double the work required. Remember lift is the difference between the chilled water supply and either cooling tower supply or ambient dry-bulb air temperature. Since air-cooled chillers must raise the refrigerant temperature above the ambient dry-bulb temperature, they consume more power.
Both chiller types will improve chiller performance when the lift is reduced. This is often referred to as condenser relief. Figure 29 shows the annual dry-bulb vs. wet-bulb temperature for Chicago. The curves show the amount of available condenser relief for each type of chiller. As expected, the wet-bulb based (water-cooled) chillers offer the best performance at design conditions, however, the relief during spring and fall seasons quickly reduces the difference. In the winter, there is no advantage, as either system will operate at the minimum condensing temperature permissible by the refrigeration system.
Understanding the overall annual performance is important when considering building use. For example, schools are rarely operating at design conditions during the summer months due to reduced occupancy. This has the effect of limiting the advantage water-cooled chillers have over air-cooled chillers.

Water-cooled chiller systems usually outperform air cooled chiller systems. However, when considering life cycle analysis, the payback for water-cooled systems can be very long
1.2 Air Cooled Chiller System Design
Air-cooled chillers will affect the system selection and design details. In most cases, air-cooled chillers are limited in evaporator shell arrangements when compared to centrifugal chillers. They are designed to work well around the AHRI 550/560 design conditions (54°F EWT, 44°F EWT). The design temperature range should stay within 20% of these operating conditions. Series chiller arrangements will typically double the flow and half the temperature change in the evaporator. This can lead to very high water pressure drops. Contact your sales representative to review the acceptable performance ranges of the various chiller options.
Air-cooled chillers can be used in any chiller system design. They are commonly used in single, parallel, and primary-secondary systems. They can be mixed with water-cooled chillers in multiple chiller applications.
Most air-cooled chillers can be used in either constant or variable flow applications. Variable flow in the evaporator is a function of the staging and chiller controller. Check with your sales representative when designing variable primary flow systems.
There are many applications that require a small amount of chilled water during the winter. For example, a hospital might require chilled water to cool an MRI year-round while the AHUs can switch to airside economizers in the winter. When there is a requirement for small amounts of chilled water in winter, an air-cooled chiller is an excellent solution. An air-cooled chiller avoids the need to operate a cooling tower in cold (freezing) weather. In addition, the air-cooled chiller will offer equal performance to a water-cooled chiller at low ambient conditions.
Parallel air cooled chiller systems can be as energy-efficient as water-cooled systems when the ambient air dry bulb temperature is cool: around 60°F or below. If the system total load in a dual chiller plant is above 40% both chillers should be operated at part load. For system loads below 40%, which often correspond to lower ambient dry bulb temperatures, a constant flow system should run with only one chiller operating since the chiller performance at cool ambient dry bulb temperatures is very good.
Parallel air-cooled chillers in variable primary water loops should also have variable speed compressors as well as variable speed condenser fans. In this case, both chillers should run at all operating plant load ratios.
1.3 Water Cooled Chillers
Water-cooled chillers vary in size from 5 tons to more than 3000 tons. They use scroll, screw, and centrifugal compressors to accomplish this. Most operate on R-410A, R-134A, or R-123, with R-22 still being used in developing countries.
Water-cooled chillers need a source of condenser water. In some applications, this water comes from a river or ocean. Where salt water is used, the chiller should be isolated with a heat exchanger to protect against corrosion. This will raise the condenser water temperature by whatever the approach is for the heat exchanger. Alternatively, there are special modifications that can be made to the chiller to allow the saltwater to pass through the condenser barrel. Modifications include titanium tubes and special treatment of the tube sheets.
Water-cooled chillers use scroll or screw compressors up through 400 tons. Scroll chillers usually have multiple compressors in one or two refrigeration circuits. Control is provided by staging the compressors. Large chillers typically use single or multiple screws or centrifugal compressors. Screw compressors vary the capacity by modulating the flow. To improve part-load performance, the use of VFDs and inverters are becoming more common.
1.4 Magnetic Bearing Centrifugal Chillers
Large water-cooled chillers use centrifugal compressors. Centrifugal compressors provide very high refrigerant flow rates at moderate lift conditions found in water-cooled applications. These compressors can be more than 3000 tons, with the prime movers (motors) exceeding 2000 horsepower. Centrifugal chillers are a dynamic type and behave similarly to centrifugal fans. The compressor imparts velocity pressure to the refrigerant and then converts the velocity pressure to static pressure. a more thorough explanation can be found in Daikin
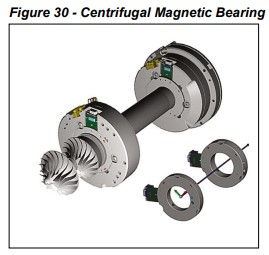
Applied AG 31-002, Centrifugal Chiller Fundamentals or Daikin Applied Fundamentals of Refrigeration.
Traditional centrifugal chillers use roller bearings and hydrodynamic bearings; both types of bearings consume power, and both require oil and a lubrication system. This reduces the efficiency in the system and increases the operating costs of the chiller due to a few different factors. The first is that there is still friction present, even with the oil. This creates heat along with an increase in needed energy to overcome that friction. The second factor is oil degradation. All oil lubricated chillers will deposit oil on heat transfer surfaces and eventually lose efficiency. A typical percentage of performance degradation is 8% with values up to 15% in some extreme cases. This contributes to the large use of energy over the life of the chiller. A third factor is the amount of maintenance needed for the chiller. Annual and semiannual maintenance is needed to keep the chiller operating efficiently. Maintenance procedures include cleaning tubes and oil maintenance. Some of these oiled chillers have implemented special designs to keep the chiller as efficient as possible even with using oil in the system.
The next generation of centrifugal compressors includes a frictionless magnetic bearing (Figure 30) for oil-free operation. The use of the magnetic bearing reduces friction in the chiller resulting in not only being a more efficient chiller, but also a quieter, easier to maintain, and more reliable chiller. Because the compressor is being supported by magnetic bearings, the chiller’s efficiency at part load is much higher than other chillers. Recall from Chiller Basics, that using a high efficiency at part load chiller is very important because the chiller will operate at below full load 98% of the year. This results in the overall operation cost of the chiller is much less than other chillers.
2.0 Winter Operation
In climates where freezing conditions exist, winter operation must be considered. There are two issues to deal with. The first is the necessary changes to the chiller to operate in cold temperatures. All chillers have a minimum condensing temperature. Going beyond that temperature may damage the chiller. For air-cooled chillers, the condensing fans are staged off or slowed down to maintain the correct condensing temperature to protect the chiller. There are other changes that are required as well, such as larger crankcase heaters. Consult your sales representative to discuss these requirements.
Winter operation for a water-cooled chiller must also be considered. Winter operation has the advantage of using waterside free cooling due to the cold outdoor ambient conditions and not even running the chiller. However, recall from Cooling Tower Basics, if the chiller needs to be run, the minimum temperature the condenser water can be is 65°F for most chillers. Special chiller controls can account for bringing the condenser water temperature up to an acceptable operating temperature.
The second issue is protecting the chilled water from freezing. Here are some possible solutions:
Heat trace the piping and evaporator. This is a good solution where freezing weather occurs but is not extensive. It is also a good backup for systems that are to be drained in the winter. Many chillers already include evaporator tracing. Check with your sales representative.
Add antifreeze. A common solution is to add either propylene or ethylene glycol to the chilled water. While this will resolve the freezing issue, it will increase pumping work and de-rate both the chiller and chilled water coils. Maintaining the correct level of antifreeze in the system becomes an additional maintenance issue. A loss of antifreeze in the system due to flushing or a leak and subsequent water make-up can allow the chilled water loop to become vulnerable to freezing. Adding glycol to a system that was not designed to have it must be carefully examined to ensure the system will operate properly.
Relocate the evaporator barrel inside the building envelope. Relocating the evaporator avoids antifreeze but will require field refrigerant piping. There are also limitations on piping distances and elevation changes. Consult your sales representative to discuss the details.
Use an indoor chiller with a remote air-cooled condenser. This arrangement will require mechanical room space, however, the equipment can be serviced from within the building. This is a very good solution for very cold climates.
Use of a sump heater for water-cooled systems will prevent freezing in the tower but allow the chiller to be available for operation in the winter.
Use an indoor remote sump. This has the advantage of bringing the condenser water indoors and keeping the water warmer than a sump heater can keep it – making start-ups less problematic. There’s also less risk of a sump heater failure and a freezing situation in the tower. It is common to use a three-way diverting valve to allow water to bypass directly from the chiller to the sump. This will assist the chiller during light load startups.
The design of these air-cooled chillers by the HVAC Contractor Hobe Sound company is impressive. The sleek and compact structure not only enhances aesthetics but also ensures efficient space utilization, making it suitable for various installations.