Dual Compressor and VFD Chillers
- Scholenberg
- Dec 7, 2021
- 5 min read
The unique performance of both Daikin Applied dual compressor and variable frequency drive chillers affect the chiller plant design. While it is satisfactory to simply switch conventional chillers with either dual or VFD chillers in the chiller plant, to take full advantage of these chillers capabilities, the design should be modified.
1.0 Dual Compressor Chillers
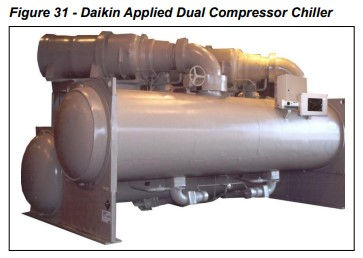
Daikin Applied’s dual compressor centrifugal chillers (Figure 31) offer many advantages over conventional single compressor chillers. From a performance point of view, the chiller is most efficient at 50% capacity. At this point, only one compressor is operating with the full evaporator and condenser surface areas available for heat transfer. This dramatically lowers the amount of energy that the chiller is using, while still maintaining the load. The built-in redundancy of a dual compressor chiller allows the designer to use fewer chillers and still provide the owner with backup equipment. The dual compressor configuration also allows maintenance on one of the compressors while having the capability of maintaining 50% of the building load. This can save considerable capital expense in installation costs along with a reduction in downtime for maintenance.
2.0 Variable Frequency Drives
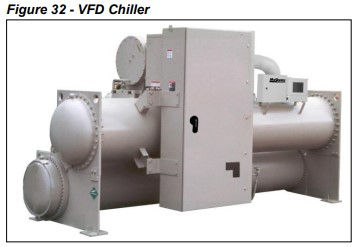
Water-cooled chillers with a VFD (Figure 32) use a combination of the VFD and inlet guide vanes to modulate the capacity of the chiller. The VFD is used to change the speed of the compressor and the inlet guide vanes control the quantity of refrigerant. For information on how this works, refer to Daikin Applied AG 31-002, Centrifugal Chiller Fundamentals.
Air-cooled chillers can also use a VFD to modulate the capacity of the chiller. Screw chillers that implement a VFD use the VFD to change the speed of the compressor while using a slide valve to modulate how much refrigerant enters the compressor.
The performance savings gained with a VFD are achieved at part load. The use of a VFD will increase the amount of energy used at full load because it takes energy to run the VFD. The VFD can only be used when the lift on the compressor is reduced. Lift in a water-cooled chiller is reduced when the chiller load is decreased or when the condenser water temperature is lowered and/or the chilled water temperature is raised. In an air-cooled chiller, the lift is reduced when the ambient temperature is lower than the design day. When the lift is reduced and the VFD is used, the chiller will operate much more efficiently at part load than a conventional chiller does because of its ability to modulate the compressor.

The best way to take advantage of a water-cooled VFD chiller is to reduce the condenser water temperature as much as possible. Climates with reasonable annual changes in wet-bulb are prime candidates for VFD chillers.
VFDs also provide benefits on the electrical characteristics of the unit. They provide lower starting currents compared to the traditional starters that are used, as seen in Figure 33. This feature can help to reduce the electrical installation costs, especially if the chiller is powered by emergency generators. The lower inrush current requirements typically allow the owner to downsize the capacity of the emergency generator.
3.0 System Design Changes
3.1 Conventional Application
Both dual compressor and VFD chillers operate much more efficiently at part load. Conventional chillers operate most efficiently at or near full load. To fully optimize a dual or VFD chiller, the design should take advantage of its part-load performance because a building spends the most operating hours at part load conditions.
Figure 34 is based on two equally sized chillers in a primary/secondary arrangement using the AHRI condenser relief profile for the entire plant. At the 50% load point, the second chiller must be started. For conventional chillers, the chiller performance drops because the load is split evenly between the two chillers and they unload to a less efficient operating point. The dual and VFD chillers actually improve their performance because the chillers are unloaded and there is condenser relief available.
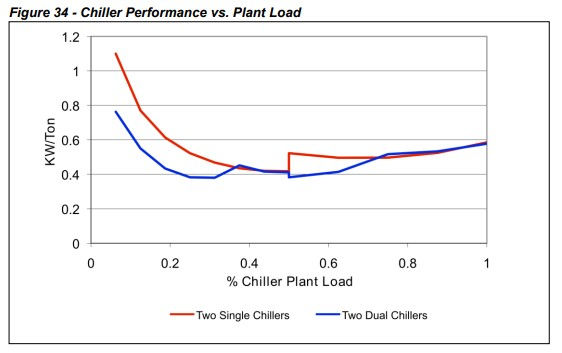
Considering that most buildings experience a significant number of operating hours around 50% plant load, the dual or VFD chillers may offer appreciable savings even when used in a conventional manner.
3.2 Lead Chiller Application
The first chiller that is activated in a plant, typically called the lead chiller, operates for many hours at reduced load and condenser water temperature. An example is a multi-chiller primary secondary plant. The lead chiller sees optimal conditions for either a VFD or a dual compressor chiller. The other chillers in the plant can be conventional chillers. Each chiller that is started as the plant load increases will operate at a higher per cent load with less condenser water relief and therefore will offer fewer savings.
3.3 Winter Load Application
Another good application for a dual or VFD chiller is winter load applications. Building using fan coils have considerable chiller plant loads even in winter. Other buildings such as hospitals or office buildings with computers, telecommunication, or other winter chilled water loads can also take advantage of a dual or VFD chiller. In many cases, these winter loads are relatively small. Conventional thinking would require a smaller chiller sized specifically for the load. With a dual or VFD chiller, there may not be a performance penalty to use a larger chiller sized for summer loads to handle the small winter load. The peripheral loads such as pumps should be checked when evaluating performance.
3.4 Series Chiller Application
A common method for sizing chillers used in series is to select both chillers to be able to perform as the lead chiller. This causes the lag chiller to be sub-optimized because the lift is reduced in the lag position. By using a VFD chiller as the upstream chiller, the VFD can take advantage of the reduced lift when operating as the lag chiller. In addition, the same chiller can be used as the lead chiller during light loads when there should be condenser water relief available.
3.5 Asymmetrical Chiller Application
Selecting the chillers to be different sizes can improve chiller plant performance based on the building load profile. Using either a dual or VFD chiller for that larger chiller can enhance the savings. Consider a 1200-ton plant consisting of an 800-ton dual compressor and a 400-ton single compressor chiller. The dual compressor chiller can accommodate the plant load up to 800 tons. Above that, the second chiller must be started and both chillers will initially operate at 67%. The larger chiller will be more efficient when unloaded.
3.6 Low Delta T Application
Most variable flow chiller plants will see a drop in return water temperature as the load drops. The low delta T can cause serious operation issues with the plant. One solution is to use either dual or VFD chillers and operate two chillers at part load as opposed to one chiller fully loaded. The dual or VFD chillers partly loaded should be more efficient than one conventional chiller fully loaded. The chiller savings can be used to offset the additional pumping cost from operating peripheral pumps. Moreover, this arrangement will provide the necessary chilled water flow on the primary side to offset the low delta T problem.
3.7 Total System Analysis
When estimating the savings, consider both the type of chillers used and the available lift reduction (condenser relief) and peripheral equipment that must be operated. Simulations can be run to determine the best possible solutions.
Comments