HVAC- Primary Secondary Systems
- Scholenberg
- Dec 12, 2021
- 12 min read
For large chillers or where more than two chillers are anticipated a primary-secondary (also called decoupled) piping system is often used. To reduce installation and operating costs, it is desirable to apply diversity to the system flow. With diversity applied to flow, the pumps and piping will be smaller. To accomplish this, two-way control valves are used at the loads. At the same time, it is desirable to provide constant flow through the chillers to maintain chiller stability. The solution is primary secondary piping.
1.0 Basic Operation
Figure 42 shows a 400-TR primary-secondary system with four chillers. The system is operating at 67% or 268 TR. The 268-TR load requires 643 USgpm (10 USgpm/ton). Three chillers are operating along with their 240 USgpm primary pumps.

The additional flow, 77 USgpm, from the three primary pumps bypasses the building through the decoupler. The bypassed water mixes with the return water from the building and is returned to the chillers. The chillers operate at the same per cent load.
2.0 Basic Components
21. Chillers
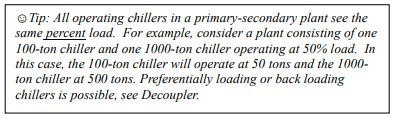
Figure 42 also shows a typical primary secondary chiller plant with four chillers. There can be any number, size, and type of chillers in the system. Different capacity chillers are acceptable and can be advantageous depending on the load profile. The only requirement is that all chillers must operate on the same chilled water temperature range. Unless specially configured, all operating chillers will have the same per cent load.
2.2 Primary Pumps
Primary pumps provide constant flow through the chillers. They can be dedicated to each chiller as shown or there can be a primary pumping plant providing constant flow to each chiller. Primary pumps can utilize a common header (See Figure 43) to allow a particular pump to serve several chillers. The advantage is should a pump fail, the chiller can still be used by activating one of the other pumps. A spare pump can also be built into the arrangement. The disadvantage to headered primary pumps is complexity and cost.

If the chillers have different flow requirements, meaning they are different sizes, then intermixing pumps becomes even more complicated. It can be done using VFDs on the pumps. The BAS can be preprogrammed with the appropriate pump speed required to deliver the correct flow to each chiller. This allows each chiller to receive its correct flow rate.
The flow for each chiller is based on the design flow required by the chiller. The flow is only provided when the chiller is operating. An automatic isolating valve is required for each chiller to stop short-circuiting when the chiller and pump are off. Primary pumps need only provide enough head to move chilled water through the chiller and the piping pressure drops between the chiller and the secondary pumps. Pump head values in the range of 25 to 75 ft are common.
2.3 Condenser Pumps
If the chillers are water-cooled, each chiller will have a condenser pump and cooling tower or another form of heat rejection device. Like the primary pumps, the condenser pumps can be dedicated to each chiller as shown or a condenser water pump plant can provide condenser flow. The flow rate to each chiller is typically constant and based on the design flow rate for the chiller. Where the head pressure drop is particularly high, variable flow condenser pumps may offer additional savings and are becoming more common in chiller plant design.
2.4 Cooling Towers
Cooling towers can be grouped or individual. Individual towers allow the tower to be sized specifically for the chillers needs, which can be important in hybrid chiller plants. Cooling towers are covered in Cooling Tower Basics.
2.5 Secondary Pumps
Secondary pumps are variable flow and sized to provide flow throughout the chilled water plant. In a sense, they handle all the pressure drops “outside the mechanical room”. Refer to Variable Flow Pumps on how to vary the flow through pumps.
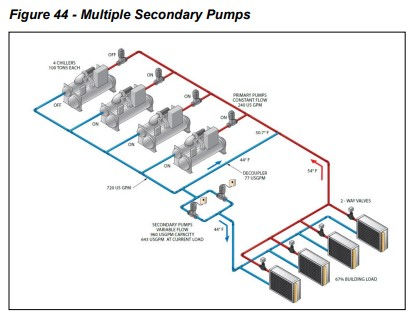
Most secondary pump arrangements include multiple pumps and often a spare pump as seen in Figure 44. Systems can also have multiple loops in the secondary system. These will serve areas with different operating schedules or widely different fluid pressure drops (such as a building on the far side of campus). The individual loops can be scheduled off when not required. A good system design should always group loads with common pressure drop and scheduling requirements to reduce pumping work.
2.6 Decoupler
Referring to Figure 44, it would appear that the primary and secondary pumps are in series. This is not the case, however, because of the decoupler. The decoupler allows the pumps to operate at different flow rates. This is necessary because the primary pumps are fixed speed and the secondary pumps are variable speed. Only on special occasions will the primary pump flow and the secondary flow be equal. An example would be when the cooling load (and secondary flow) can be met by a fully loaded chiller.
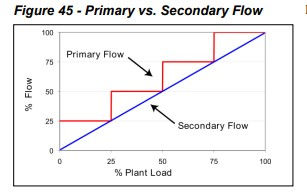
Figure 45 shows primary flow vs. secondary flow. The secondary flow is based on the load in the building. Specifically, the secondary flow rate is produced to maintain the necessary system pressure differential. The primary flow must always meet or exceed the secondary flow. Any excess primary water flows through the decoupler to the return side and back to the chillers. Any time the primary flow is less than the secondary flow, warm return water will flow “backwards” through the decoupler and mix the primary flow going out to the building.
2.7 Decoupler Sizing in Primary Secondary Loops
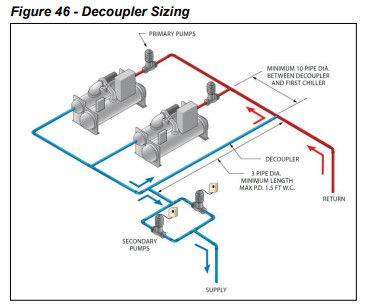
Decouplers should be sized for the flow rate of the largest primary pump. This may be more than the design flow rate of the largest chiller if overpumping is being considered. The pressure drop should not exceed 1.5 ft. As the pressure drop through the decoupler increases, it tends to make the primary and secondary pumps behave like they are in series. To avoid thermal contamination, the decoupler should be at least three pipe diameters in length. Longer decouplers tend to increase the pressure drop. When the secondary return flows straight through in the tee to the primary return, there should be at least 10 pipe diameters to the first chiller. This is to help avoid the possibility of having stratification in the primary return line, which can lead to unmixed water to the first chiller. This can lead to chiller cycling.
2.8 Decoupler Location
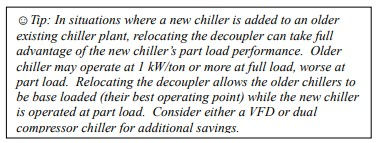
The location of the decoupler line will change how the chillers are loaded. Figure 46 shows the typical layout with the decoupler between the chillers and the load. In this situation, each chiller sees the same return water temperature even at part load conditions. Figure 47 shows the decoupler line in a different location. Locating the chillers between the secondary loop and the decoupler line causes the return water temperature to each chiller to vary. This is often referred to as “backloading” or “preferentially” loading the chillers. Chiller 2 in Figure 47 will see close to the secondary loop return water temperature. Chiller 1 will see a mixture of supply water and return water. As a result chiller, 2 is more heavily loaded than chiller 1.
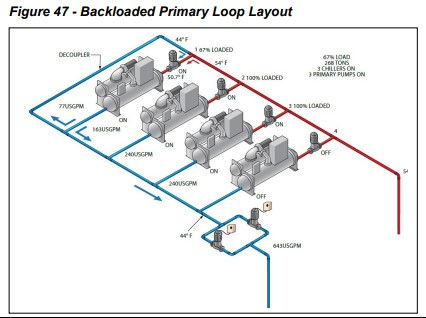
Relocating the decoupler can make sense if one or more of the chillers is a dual compressor model or if there is a VFD on the compressor. These types of chillers have very good part-load performance. By locating one of these types of chillers close to the decoupler line, and the better full load chiller furthest away, the strengths of each chiller can be maximized. Another application for backloading chillers is where one of the chillers is a heat recovery type, Daikin Applied’s Templifier™, which is connected to the condenser loop. In this case, providing additional load to that chiller provides a heat source for the energy recovery process. Decouplers should be sized for the maximum design chilled water flow through the largest chiller. Their length should be as short as possible to minimize pressure drop.
2.9 System Expansion
Primary/secondary piping allows easy expansion both in the chiller plant (primary loop) and the building (secondary loop). To expand the chiller plant capacity, another chiller can be added to the loop. By strategically locating the decoupler and the new chiller (see Figure 47), it is possible to apply a greater load on the new chiller. This can be advantageous if the new chiller is more efficient than the rest of the plant. If the building load is increased, a new loop can be added. The pump for the new loop can be sized to meet the new loop’s pressure drop requirements.
2.10 Tertiary Pumping

There are two key applications where tertiary piping is helpful. The first is where the pressure available in the secondary loop is not sufficient for a specific load. The second is where a load requires a different temperature range than the main system. Figure 48 shows a tertiary pumping system. To localize pumps, a third loop for the pumps is installed. The tertiary pumps will handle all the head requirements of the different towers. This has the advantage that, if there is a new load attached to the building, the tertiary pumps can handle this new load. The arrangement in Figure 48 includes the tertiary pumps and two-way control valves. The tertiary pumps provide the necessary flow and head for the facility it serves. If the two-way valves begin to close, the pumps will begin to slow down. The secondary pumps will also be able to be slowed down. The flow reduction in the pumps will create savings in energy for the system. Another key advantage of this arrangement is the tertiary loop does not have to have the same temperature range as the main loop. The design chilled water temperature in the tertiary loop must be warmer than the main supply chilled water temperature. If they are the same temperature, the two-way valve will open and bleed supply water into the return line leading to low delta T syndrome (See

Low Delta T Syndrome Causes and Solutions). The two-way valve should control to maintain the tertiary loop supply temperature (approximately 2°F warmer than the main loop) and should close when the tertiary loop is not in operation to avoid unnecessary crossflow.
2.11 Varying Chiller Sizes
One advantage of primary/secondary systems is varying the chiller sizes. As long as the supply water temperature and the design delta T are the same, the chillers can have different capacities. Varying the chiller sizes allows chillers to be selected so the chiller plant is at maximum performance when the run-hours are highest. For example, consider a chiller plant where two chillers can be used. The bulk of the run-hours will be at 50% to 70% of design capacity (At part load conditions). This will require the two equally sized chillers to operate between 50% and 70% of their design capacity. By varying the chiller sizes to one at 700 tons and one at 300 tons, the system load can be met with one chiller for the bulk of the operating time. The savings come from operating one chiller at near full load conditions over two chillers at part load conditions and from avoiding operating additional ancillary devices such as primary and condenser pumps. During the spring and fall seasons, the operator has the option of using the chiller whose size best fits the expected load. For instance, on a light load day, the smaller chiller can be used. The chiller will be more fully loaded than the larger chiller offering a performance improvement for the chiller. In addition, the smaller primary condenser pump and tower fan will be used offering ancillary equipment savings
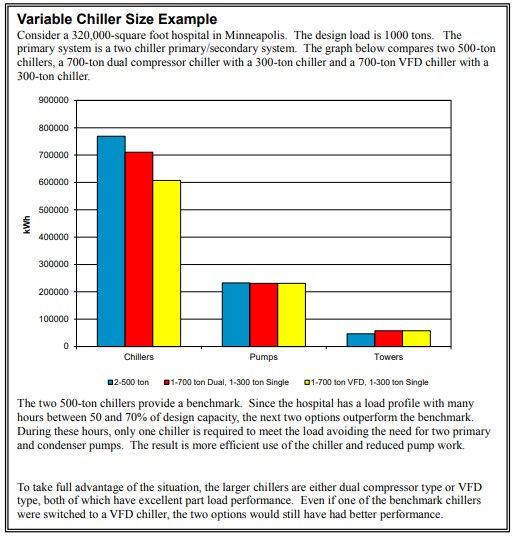
3.0 Very Large Chiller Plants
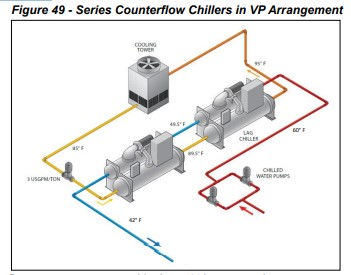
Very large chilled water plants follow the same basic design considerations discussed so far. The scale of large chiller plants, however, creates some trends that should be addressed. Large plants tend to use large (18°F or greater) chilled water ranges to reduce pump and piping sizes and pump work. This in turn requires lower chilled water temperatures to offset the effect on the cooling coils (see Water Temperatures and Ranges). Figure 49 shows series counterflow chillers in a variable primary system. The series counterflow arrangement provides an efficient means to produce 40°F supply water with an 18°F temperature range. The series counterflow arrangement can provide about 5% better annual performance than single large chillers when using large temperature ranges. The variable primary arrangement provides variable flow in the system to reduce pipe size and pump work.
3.1 Chiller Plant Sequence of Operation
Chiller plant operation can become very complex. It is not unusual to have dedicated and specialized building automation systems to operate the chillers and the ancillary equipment. While a complete discussion on the many ways of operating a complex plant is beyond the intention of this guide, here are a few key areas to consider:
3.1.1 Condenser Pump and Cooling Tower Operation
Whenever a chiller is online, there will need to be condenser flow and a means to cool it. With dedicated pumps and towers to each chiller, this is straightforward. They can be operated by either the chiller control panel, assuming it has outputs, or by the BAS. The chiller control panel may offer better performance since it has an intimate understanding of the needs of the chiller. Using the BAS to operate the equipment makes the operation easily visible to the control system and to the operator. (For example, without an additional flow sensor, it may not be obvious to the BAS that the condenser pump is operating.) Using an open protocol allows the chiller to operate the equipment while providing easy visibility for the BAS and operator. The information is passed digitally from the chiller controller to the BAS. When the condenser pumps are shared in a common header the sequence becomes more complex. Automatic isolation valves will be required. If the pumps are all the same size, the BAS must open the valve and start a condenser pump. The pump sequence is usually based on pump run-hours. When the chillers have different condenser flow requirements, the system becomes very complex. Flow meters may be required. When a common cooling tower plant is used, a sequence to determine the optimum condenser water temperature is required.
3.1.2 Primary Pump Operation
Primary pumps will have similar issues as condenser pumps. Dedicated pumps are straightforward, while common pumps in a headered arrangement can be more complex. When over pumping is considered as a solution to low delta T syndrome or to take advantage of additional chiller capacity during low lift situations, the sequencing can be very complex.
3.1.3 Secondary Pump Operation
Secondary pump operation, in general, is covered in Variable Flow Pumps.
3.1.4 Chiller Staging
A critical requirement of a primary secondary system is that the primary flow always be equal to or exceed the secondary flow. Theoretically, this should happen because the chilled water temperature range is constant and the chilled water flow is proportional to the cooling load.

Assuming this happens, chillers can be staged on and off based on their load. However, this is not necessarily a good control scheme. First, low delta T syndrome can cause a disconnect, so the chilled water flow is not proportional to load. (See Low Delta T Example). Just using chiller load will not recognize when this situation occurs. A second issue is the chiller power draw is not an exact indicator of the actual cooling effect. For instance, if there is condenser water relief, the chiller will produce the required cooling effect with fewer kilowatts. It is even possible for the chiller to produce more than the design cooling capacity with the same kilowatts if there is some form of condenser relief. Monitoring the chiller power load can provide some guidance in chiller staging along with other data inputs discussed below. Power monitoring can be accomplished by using open protocol communication gateways or with power meters. To make sure the primary flow meets or exceeds the secondary flow, the BAS must also monitor chilled water flows. One method is by measuring the direction of flow through the decoupler. A flow meter in the decoupler can be difficult due to the short pipe length and low flow rates. It is important that if a flow meter is used, that the flow is verified so that it provides meaningful information. Another method is to measure the chilled water temperature in the decoupler. A single temperature sensor in the decoupler in principle should work. For instance, if the temperature is near the supply water temperature setpoint, then flow must be going from the supply to the return (which is what is required). However, if the temperature rises to close to the return water temperature, then the flow must have reversed (which is not desirable). In practice, a single sensor can lead to false readings for several reasons. For example, low delta T syndrome can make the actual chilled water temperature range very small so the BAS cannot tell which way the water is flowing. A more reliable method is to use temperature sensors in the supply and return piping on both sides of the decoupler. This arrangement allows the BAS to monitor the actual chilled water temperature range at the decoupler. With four sensors, the BAS can monitor that the chilled water temperature before and after the decoupler on both the supply and return. This ensures that the supply water temperature does not rise as it passes the decoupler. Once the situation occurs where there is reverse flow in the decoupler, another chiller and primary pump must be added to keep the chilled water plant operating properly. Using temperature sensors may not provide very much warning. Another method for staging chillers is to use a flow meter in the chilled water supply line downstream of the decoupler. Using the required flow and the flowrates for each of the primary pumps (these are fixed flow rates), the BAS can monitor if there is enough primary flow for the required secondary flow. This method is very reliable. It can also provide some warning that another chiller and primary pump is going to be required. Normal schedules have the next chiller start when the current chiller has been operating at 90% capacity for 30 minutes. The actual load and time period vary from project to project. Many operators do not want a chiller to automatically start but prefer that the BAS indicate a chiller is required. If the operator acknowledges the start request, the BAS can then enable another chiller.
3.1.5 Optimizing High Part Load Performance Chillers
High part load performance chillers, such as a chiller with a VFD or a dual compressor chiller, may create an opportunity to operate the chiller plant in a more efficient manner. These chillers operate more efficiently at part load than at full load. To take advantage of this, partial loading of multiple chillers to meet the load may use less energy than running a single chiller at full capacity. More complex operating algorithms may be required to optimize these systems. For more information on high-performance part load chillers, refer to Dual Compressor and VFD Chillers.
3.1.6 State of the Art Chiller Plant Operation
The previous section provides the basics to get a primary secondary system to operate satisfactorily. Leading-edge control systems are aimed at improving the overall system performance. To accomplish this, algorithms are developed that model the building load profile and monitor the weather. Threedimensional chiller models are also used along with matrices for the power consumption of individual ancillary components. The program then simulates the building load and monitors the weather conditions. It evaluates which combination of equipment will use the least power to accomplish the load. In large systems, this additional effort has been shown to pay for itself.
Comments