HVAC-Waterside Free Cooling
- Scholenberg
- Dec 12, 2021
- 7 min read
Some HVAC systems, such as fan coils, can require chilled water year-round. Where the weather allows, waterside free cooling can avoid the need for mechanical cooling. Other systems such as floor-by-floor compartment systems can use waterside free cooling and avoid the need for access to an exterior wall.
1.0 Direct Waterside Free Cooling
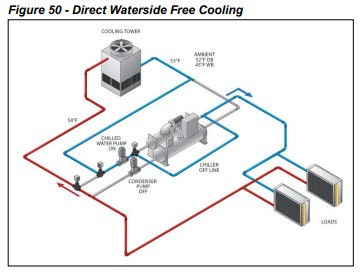
There are several ways to provide waterside free cooling. The chilled water loop can be connected by means of three-way valves, directly to the cooling tower in a “strainer cycle” method as seen in Figure 50. This method is not preferred because the chilled water loop is then exposed to the atmosphere introducing dirt and creating water treatment difficulties. The use of a heat exchanger may be used to keep the chiller clean.
2.0 Parallel Waterside Free Cooling
Figure 51 shows a heat exchanger in parallel with the chiller. During free cooling, the chiller is off and isolated by valves. The heat exchanger rejects heat into the condenser water loop. For this to happen, the condenser loop must be colder than the chilled water loop (the reverse of normal chiller operation).

Figure 51 - Waterside Free Cooling with Heat Exchanger in Parallel
This system is “non-integrated” meaning it can only be either mechanical cooling or free cooling. Nonintegrated systems generally do not offer as many savings as integrated systems but avoid additional operating hours for chillers at light loads. Continuous light load operation for some chillers can lead to operational difficulties such as oil migration or repeated starts.
3.0 Series Waterside Free Cooling
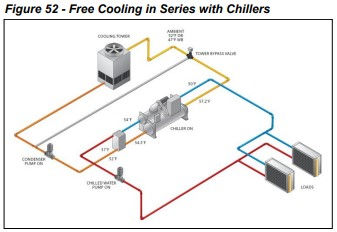
Figure 52 shows a different free cooling arrangement with the chiller in series with the heat exchanger. Since the heat exchanger operates with a higher return chilled water temperature, the operating season is longer than the parallel arrangement, offering more annual savings. This is an integrated system with the chiller “trimming” the chilled water temperature while operating with significant condenser water relief. Because the heat exchanger is piped directly in series with the chiller, the heat exchanger pressure drop must be overcome whenever the chiller plant operates. ASHRAE Standard 90.1 stipulates the maximum pressure drop that this heat exchanger can have. It is recommended that the most recent version of Standard 90.1 be referenced.

Figure 53 shows a modified version where the heat exchanger uses a small tertiary loop and a dedicated pump. This arrangement removes the heat exchanger pressure drop from the main chilled water system. Locating the heat exchanger in the main return line allows the heat exchanger to use all the return chilled water flow for all the chillers as a heat source as opposed to just the flow for a single chiller.
4.0 Waterside Free Cooling Design Approach
Designing a waterside economizer system requires knowledge of how the building will operate at part load. Variable chilled water flow systems are a better choice than constant flow because they maintain a higher return water temperature, which provides a hotter return water temperature for the heat exchanger. The following is one method for designing the system.
Calculate the building load at the ambient conditions where free cooling can support the building (changeover point). 50°F DB and 45°F wb is a common design point since it is the ASHRAE 90.1 requirement.
Establish the chilled water supply temperature required by the cooling coils to meet the load at the changeover point. Concentrate on systems serving core load areas. Generally, the only relief these zones see is in the drop in enthalpy of the ventilation air. The goal here is to “trade” the coil capacity used for cooling ventilation air in the summer for a higher supply water temperature.
Establish the return water temperature. The return water temperature is required to size the heat exchanger. The conservative solution is to re-rate all the cooling coils with the raised supply water temperature and the reduced cooling loads. Then take a weighted average to obtain the return water temperature. A simpler calculation for variable flow systems is to assume the chilled water range will remain the same and the flow will be proportional to the building load at the crossover point. For constant flow systems, the flow will be the same and the chilled water temperature range will be proportional to the load.
Select a heat exchanger. The design requirements will depend on which type of arrangement is selected. With a heat exchanger on a tertiary loop as an example (Figure 53), use the following:
o Chilled water flow rate at the crossover point.
o Chilled water return temperature at the crossover point.
o Condenser water design flow rate.
o Assume a 2 to 3°F approach for the heat exchanger.
o Solve for the entering and leaving condenser water temperature.
Confirm the cooling tower can meet the design requirements at a wet-bulb of 45°F.
5.0 Cooling Tower Sizing
Figure 54 - Cooling Tower Performance Curve at Standard Conditions
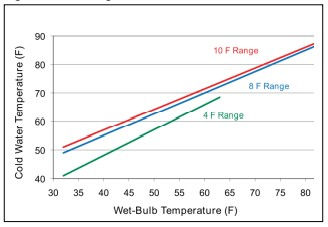
Cooling tower sizing is critical for effective operation during free cooling. Normally, the cooling tower is sized to reject the heat collected in the building plus the compressor work at design conditions. Industry-standard conditions are 95°F entering the water, 85°F leaving water and 3.0 USgpm/ton with an ambient wetbulb of 78°F. Figure 54 shows a typical cooling tower performance at industry-standard (Cooling Tower Institute or CTI) conditions for different temperature ranges. Following the 10°F range line down to 45°F wet-bulb shows the best water temperature available will be 61°F. Add to this a 2°F approach for the heat exchanger and the HVAC system would need to be able to cool the building with a 63°F supply of chilled water. Once the chiller compressors are removed from the cooling tower load, the new condenser temperature range becomes approximately 8°F. Assuming the cooling load is only 50% by the time the ambient wet-bulb has dropped to 45°F, then the temperature range now becomes 4°F. Reviewing Figure 54 for a 4°F range shows the condenser supply water temperature can now be 53°F providing 55°F chilled water. This is still very warm and it will be difficult to properly cool the building.
Figure 55 - Cooling Tower Performance Optimized for Free Cooling

Figure 55 shows a cooling tower optimized for free cooling. The cooling tower was selected to provide 48°F condenser water at a 45°F wet-bulb and 4°F range (50% building load). This allows 50°F chilled water to be produced. At summer design load conditions, the optimized cooling tower can produce 81°F at a 10°F range. Reducing the condenser water temperature to 4°F can significantly reduce the cost of the chiller and improve performance. In most cases, the saving will be enough to cover the cost of the larger cooling tower.
6.0 Waterside Free Cooling Sequence of Operation
The actual details of the control sequence will depend on which system is selected. There are several parameters, which all the systems have in common. Until the condenser water is colder than the chilled water, there can be no free cooling. During periods when free cooling is not possible, all parasitic energy losses should be minimized. Where possible, remove the heat exchanger from the system pressure drop by means of valves. Shut down any pumps associated with just the heat exchanger.
The cooling tower controls must strive to lower the condenser water temperature as much as possible. Condenser water much colder than about 65°F is too cold for a chiller. Any kind of integrated system must involve some sort of head pressure control such as a three-way bypass valve around the chiller. Once the cooling tower can no longer provide condenser water cold enough to perform any free cooling, the cooling tower control logic should change to optimize the chiller performance rather than the heat exchanger.
Many buildings go into night setbacks during unoccupied hours. When the building returns to occupied operating mode, the chiller plant can attempt to use free cooling. If non-integrated free cooling cannot meet the load, then mechanical cooling will be required.
A key issue is a transition from free cooling to mechanical cooling. Once the building load cannot be met by free cooling, the chiller will need to be started. At that point, the condenser loop will be cooler than the chilled water loop, which is “backwards” from the chiller’s point of view. To allow the chiller to operate, a cooling tower bypass line and the valve are required. The modulating bypass valve around the chiller will allow the chiller to raise the condenser loop temperature quickly and minimize the condenser water volume (thermal mass). Most chillers can control the three-way valve directly. Alternatively, the BAS can modulate the valve to reach a minimum of about 65°F as quickly as possible.
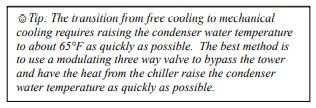
An issue with modulating the condenser flow through the chiller is the condenser flow switch will not “see” flow and this will shut down the chiller on a safety. One method to resolve this is to wire a refrigerant head pressure switch in parallel with the condenser flow switch. Below the minimum acceptable head pressure, the switch should “make” or close. Above the minimum head pressure, the switch should “break” or open. The result will be at low head pressure the head pressure switch will be closed and the flow switch will be overridden. Once there is enough head pressure, the head pressure switch will open and the flow switch can monitor the flow. While in free cooling mode, colder chilled water can produce colder supply air. In VAV systems, this can lower the supply air volumes and save fan work. For constant volume systems, colder air is of no value and the minimum chilled water temperature should be the summer design supply water temperature. Once this temperature is reached, the cooling tower fans should modulate to maintain the chilled water temperature and save tower fan energy. Maintaining the condenser water temperature above freezing conditions is also important. The cooling tower fans should be staged off to maintain the condenser water temperature at 35°F minimum.
7.0 Economizers and Energy Efficiency
The goal of either airside or waterside economizers is to reduce energy usage. Economizer energy analysis requires annual energy analysis. Airside economizers should be used where possible since, in all but the driest climates, airside economizers are more efficient than waterside economizers. An exception to this is where high levels of humidification are required since humidification is expensive and introducing large amounts of outdoor air for cooling would add to the humidification load.
ASHRAE Standard 90.1 lays down some simple guidelines when it comes to both airside and waterside economizers. It presents parameters such as how big the fans can be and the general wet-bulb and dry-bulb conditions needed to cool the entire building with only economizing. The most recent version of the standard should be referenced for specifics pertaining to the aforementioned topics.
Comments