Single Chiller System
- Scholenberg
- Dec 11, 2021
- 3 min read
Single chiller systems are the easiest to design and operate but are also the least efficient chiller plant design for buildings. Moreover, they provide no redundancy; if the chiller fails, all cooling is lost. Single chiller plants require the smallest mechanical room, particularly if the chiller is air or evaporatively cooled. Water cooled or air cooled chillers can be used however, air cooled chillers do not require a condenser loop including piping, cooling tower, and pump.
1.0 Basic Operation
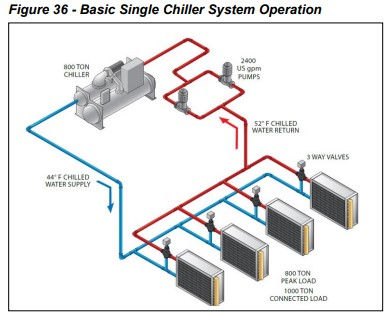
Figure 36 shows a single water-cooled chiller plant with constant flow and 80% cooling load diversity. Chilled water is circulated by the chilled water or primary pump through the chiller to the load and back to the chiller. The chilled water loop can be either constant flow or variable flow. Variable flow systems increase the complexity but offer significant pump work savings. Variable flow systems are covered in Primary Secondary Systems and Variable Primary Flow Design. A condenser loop is required for water cooled chillers. This includes a condenser pump, piping, and a cooling tower or closed circuit cooler. The condenser loop operates whenever the chiller operates.
For constant flow systems, the chilled water temperature range varies directly with the load. Depending on the load diversity, the chiller design temperature range will be less than the range seen at each load. In this case, the chiller range is 8°F while the cooling coil range is 10°F (Refer to the section on Piping Diversity). The overall result is increased chilled water pump and pipe capital cost plus higher annual pumping cost.
2.0 Basic Components
2.1 Chillers
The chiller is sized to meet the design load of the building or process. For building loads, the chiller only operates at full capacity for approximately 2% of the year. This means that for the rest of the year, the chiller is running at part load or turned off. Single chiller plant design can be used effectively if the chiller is chosen with an efficient full efficiency and an even more efficient part load efficiency. In addition to this, the dual compressor chiller design will also capitalize on the part load efficiencies, saving in operating costs throughout the year. Again the dual compressor chillers can offer complete redundancy of all major mechanical components, which resolves another issue with single chiller plant design.
2.2 Pumps
Pumps can be constant or variable flow. Pump basics are covered in the section on Pumping Basics. Both the chilled water and condenser pump must be sized for the design flow rates. Whenever the chiller operates, these pumps will operate. If the chiller has a VFD, then the pumps should likewise have the ability to throttle down the flow to maintain the minimum flow requirements of the chiller. The result is that the design chilled water and condenser flow are being pumped any time the chiller plant is operating.
2.3 Cooling Towers
Water cooled chiller systems will require cooling towers. Cooling towers and operation are covered in Cooling Tower Basics.
3.0 Single Chiller Sequence of Operation
Single chiller plants are the most straightforward to operate. Recognizing the need for chilled water is the first goal. This can be as simple as manually enabling the chiller. The process can be automated with a building automation system (BAS) which can recognize when mechanical cooling is required.

All chillers must have chilled water (and condenser water, if appropriate) flow before they operate. The simplest method is to manually turn on the pumps prior to enabling the chiller. The chiller controller, in many cases, includes a signal to operate the chilled and condenser water pumps. In this case, the pump starters can be interlocked with the chiller control panel to start the pumps. Pumps should shut down when not required to save energy. To ensure proper operation of the chiller, the pumps will be turned on, and flow will be ensured before the compressor on the chiller turns on.
Variable flow systems add another degree of complexity but also provide significant pump work savings. Control sequences for variable flow systems are covered in other sections of this guide.
In addition to operating the pumps, it is necessary to prove that there is flow. Pressure differential or paddle type switches can be used and usually are connected directly to the chiller controller. Current
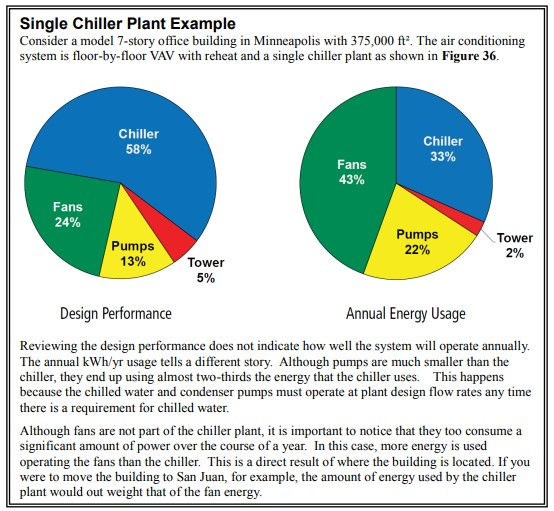
sensing devices can also be used. Operating a chiller without flow can result in serious damage. It is recommended that the manufacturer’s installation instructions be followed carefully to provide proper operation and avoid warranty conflicts.
Systems requiring a cooling tower will need to control it. Sequences for cooling towers are covered in detail in Cooling Tower Basics. Additional information on chiller plant controls can be found in product catalogs, as well as in installation and maintenance manuals.
Comments